Grande bellezza e ingegnosità tecnica rappresentano le qualità distintive che permettono ad un’opera architettonica di diventare un’icona, una figura emblematica, destinata ad attraversare i secoli lasciando una traccia indelebile nella società.
Con il loro stile unico le grandi costruzioni esercitano da sempre un fascino magnetico sull’uomo. Le loro forme iconiche e inconfondibili sono entrate nell’immaginario collettivo attraverso centinaia di film e fotografie, trasformandosi nel simbolo di città e nazioni.
Ma dietro ogni grande opera si nasconde sempre una grande storia, e con essa numerose domande. Quali sono gli elementi che la compongono? Come vengono realizzati? E quali sono i passaggi tecnici che permettono all’opera di resistere nel tempo?
Maeg apre le porte dei propri uffici e dei propri stabilimenti, raccontando le tappe che segnano il ciclo produttivo dei suoi progetti: benvenuti nel dietro le quinte del mondo maeg, dove tecnica e passione si uniscono per dare vita a opere destinate a durare nel tempo.
Processo alla base della di un progetto per definire, basandosi su norme, calcoli, specifiche tecniche e disegni, ogni dettaglio della struttura in termini di produzione e l’installazione dell’opera.
1.1 Analisi documentazione
Il processo di progettazione comincia con l’analisi delle informazioni di progetto ricevute dal Cliente,
il quale può essere un progetto preliminare - stabilisce le caratteristiche significative da dover sviluppare poi in dettaglio - oppure progetto esecutivo già specifico delle caratteristiche del materiale, dimensionali e geometriche della struttura.
Parte integrante della documentazione sono le specifiche tecniche o capitolato, ossia i riferimenti normativi a identificare i requisiti dell’opera in termini di qualità, trattamento superficiale e classe di esecuzione.
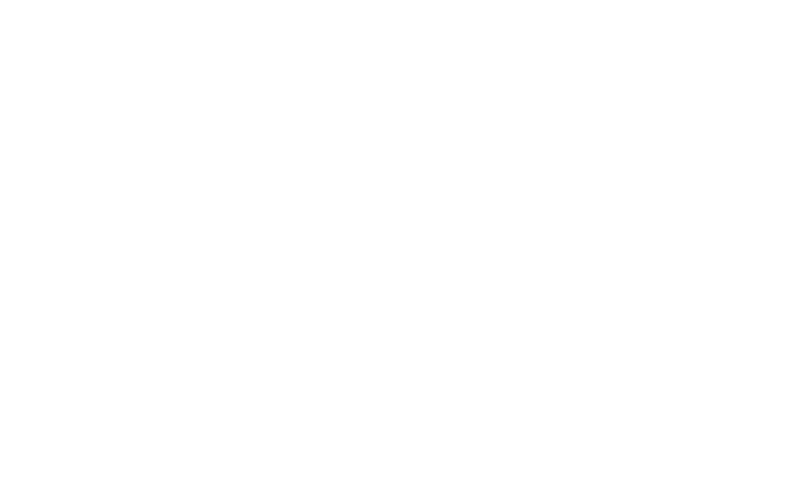
1.2 Sviluppo per la produzione
Il progetto dell’opera viene rimodellato analizzandone ogni dettaglio per realizzare i disegni costruttivi o d’officina in cui,
per ogni singolo elemento costituente della struttura, vengono definiti i dettagli come la geometria, i fori, gli spessori, gli smussi, le saldature, il numero di pezzi da produrre identificando poi ogni elemento o marca con un numero identificativo (marcatura).
Avendo definito ogni singolo elemento della struttura, dall’elaborazione dei disegni costruttivi si ottiene la distinta materiali, ossia un elenco che riassume il fabbisogno unitario, la qualità e le dimensioni del materiale da approvvigionare per il progetto.
Per ogni posizione viene elaborata la distinta di lavorazione o manualino, in cui vengono riportate tutte le lavorazioni previste in officina per poter cominciare l’effettiva fase produttiva.
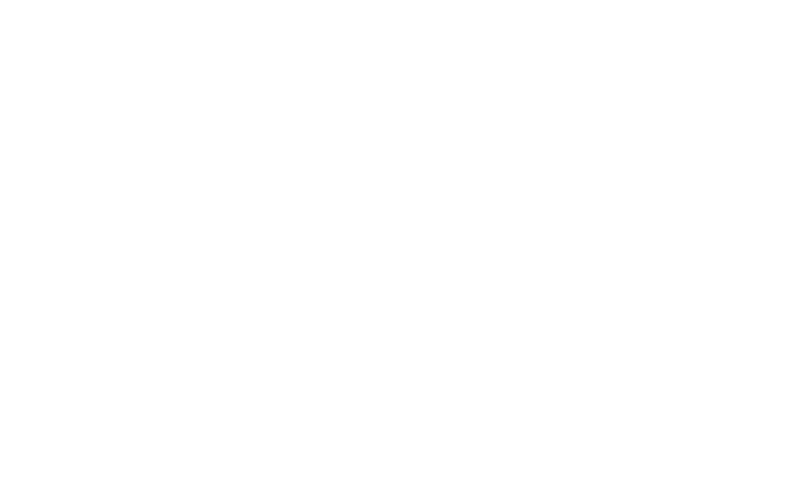
1.3 Sviluppo per cantiere
Una volta analizzati i singoli elementi minimi che compongono la struttura permettendo di cominciare la produzione si inizia a studiare un piano di montaggio per stabilire le modalità e la sequenza per unire questi singoli elementi in marche o elementi composti, tenendo conto della dimensione, costruibilità, trasportabilità, layout e spazi di cantiere, capacità di sollevamento delle gru e di montaggio in cantiere.
Considerando le diverse variabili, si inizia realizzando un modello di calcolo per verificare la tenuta strutturale dell’opera durante le diverse fasi di costruzione.
Sviluppando i singoli passaggi vengono definite le attrezzature temporanee necessarie durante la fase di installazione (banchi, torri provvisorie, etc per la quale vengono realizzati disegni esecutivi e relazioni di calcolo dedicate per poi poter procedere alla loro produzione) e mezzi di sollevamento e trasporto necessari (gru, chiatte, etc, da approvvigionare).
Una volta definita quindi la metodologia di installazione che verrà seguita in cantiere per la realizzazione dell’opera, l’ufficio tecnico redige una procedura di montaggio illustrando le diverse fasi assicurando il rispetto delle normative sulla sicurezza.

APPROVVIGIONAMENTO
Il processo commerciale che provvede alle forniture necessarie a soddisfare le esigenze per la realizzazione del progetto in base alla distinta dei materiali sviluppata dell’ufficio tecnico.
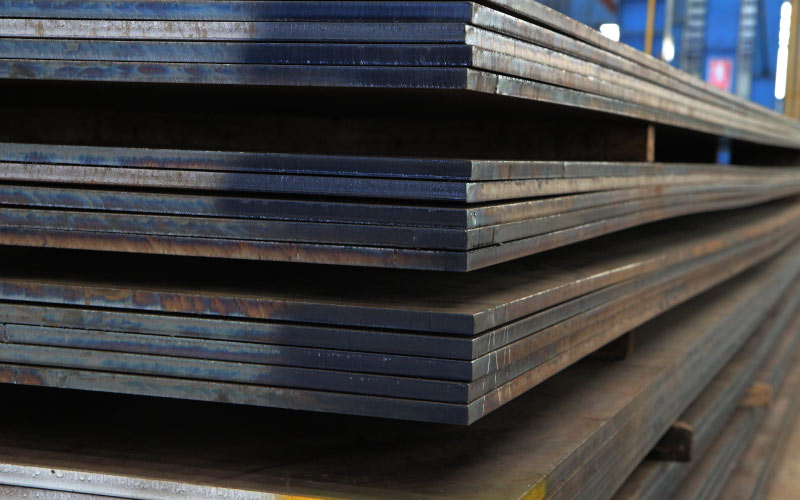
LAMIERE
Le lamiere sono lastre d’acciaio ottenute attraverso il processo di laminazione di bramme (semilavorati realizzati tramite getto per colata continua di metallo liquido in apposite forme) in cui il materiale viene passato attraverso due cilindri che lo appiattiscono fino ad ottenere lo spessore desiderato.
PROFILATI
I profilati sono prodotti trafilati a caldo detti "commerciali" in quanto seguono precisi standard internazionali riguardo alla forma della sezione della barra.
Le sezioni trasversali più comuni sono:
Sezioni "a doppio T": profilati costituiti da due piattabande parallele collegate perpendicolarmente da un’anima.
Questi profili possono essere di diversi tipi: IPE (l’altezza dell’anima è circa il doppio della larghezza delle piattabande) o HE (dove l’anima e la piattabanda hanno la stessa dimensione).
Quando le dimensioni dei profilati superano quelle standard, le travi a doppio T vengono composte da lamiere saldate.
PROFILATI
Sezioni a "U" o "C": profilati costituiti da un’anima e due piattabande raccordate in corrispondenza di una delle loro estremità, e la tipologia più comune è l’UPN.
Sezioni a "L" o angolari: profilati costituiti da due bracci perpendicolari, chiamati "ad ali uguali" se della stessa lunghezza o "ad ali disuguali" se di lunghezza diversa.
PRODOTTI CAVI
Tubi tondi, ottenuti mediante estrusione o saldatura longitudinale, oppure tubi quadri o rettangolari, ottenuti per piegatura e successiva saldatura o trafilatura.
PIOLI
Connettori impiegati soprattutto nelle strutture composte acciaio-calcestruzzo dei ponti per creare un effetto collaborante tra i due materiali attraverso la testa del piolo, la quale ha un diametro più grande rispetto al quello effettivo del gambo.
BULLONI
Elementi di giunzione smontabile, formato solitamente da un elemento maschio (vite), da un elemento femmina (dado) e da una o più rondelle, utilizzate per migliorare il bloccaggio e distribuire il carico di serraggio su una superficie più estesa.
Oltre che per dimensioni, i bulloni si differenziano per classe di resistenza: vengono solitamente impiegati quelli di classe 8.8 (alta resistenza) e 10.9 (altissima resistenza).
VERNICE
Considerata la superficie della struttura e l’ambiente naturale in cui viene installata, si calcola l’approvvigionamento della quantità necessaria e si procede con l’approvvigionamento.
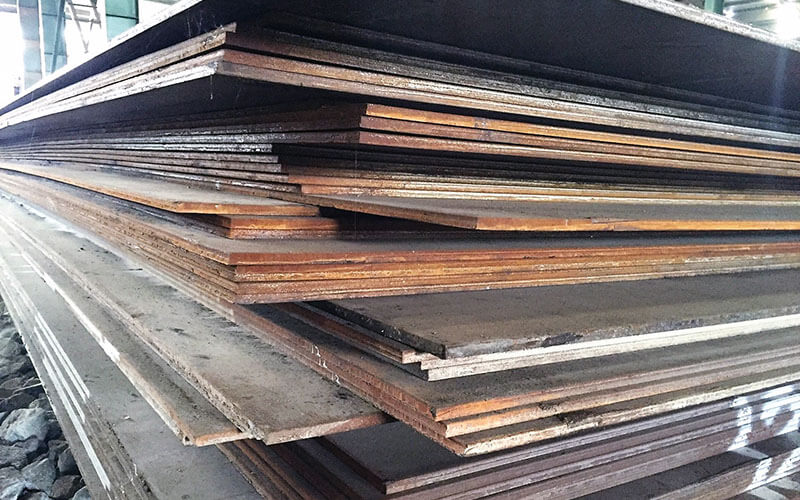



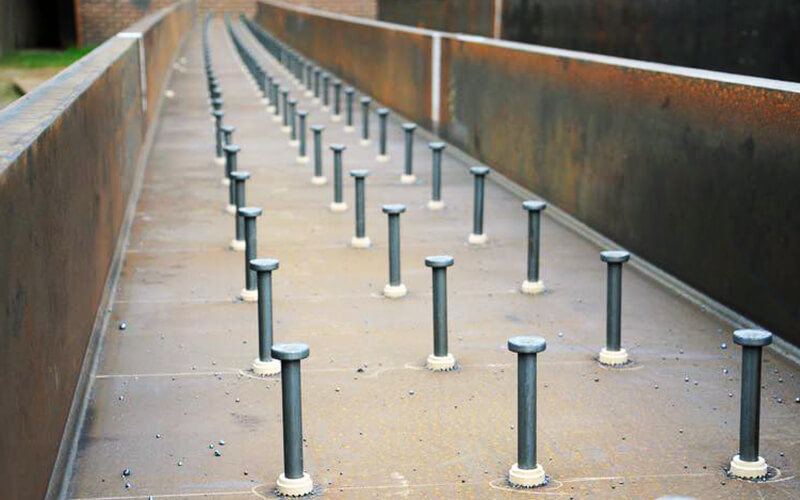
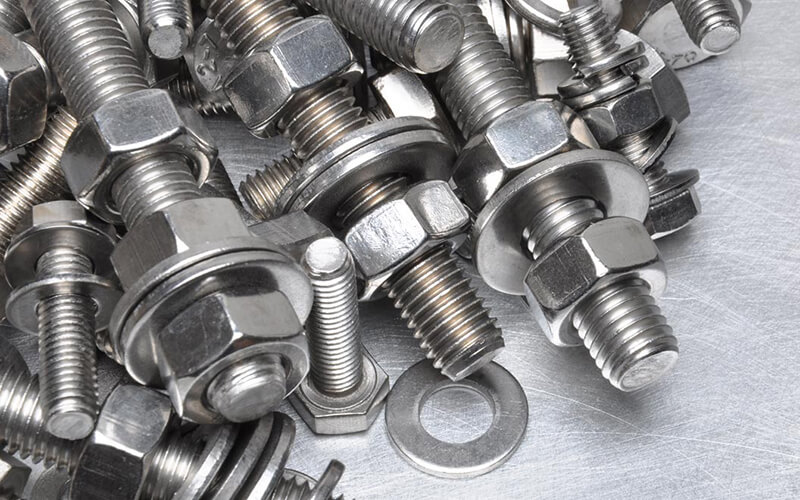

Le attività di pre-lavorazione consistono nella realizzazione dei singoli elementi della struttura (o posizioni) attraverso l’ausilio di macchine a controllo numerico (o CNC - Computer Numerical Control).
2.1 Accettazione materiale e nesting
La materia prima viene spedita nello stabilimento e viene smistata secondo le priorità di produzione nell’area di stoccaggio e trasportata nelle campate di lavorazione con l’ausilio di traverse magnetiche.
L’inizio delle attività prevede l’analisi del piano di taglio o nesting, ossia l’analisi per l’ottimizzazione del taglio sagomato delle lamiere minimizzando gli sfridi (o scarti di produzione) secondo i normalini prodotti dall’ufficio tecnico:
il nesting immagazzina i dati di ogni marca come dimensioni, spessore e le relative lavorazioni.
2.2 Taglio
Una volta stabilito il piano di taglio comincia l’effettiva fase di taglio sia su lamiere, tubi e angolari.
Il taglio può essere al plasma quando il taglio avviene tramite la ionizzazione dell’aria tra la torcia e la lamiera, creando una fiamma che raggiunge i 20.000° C e polverizza l’acciaio.
Generalmente, gli spessori di taglio sono limitati, quindi il taglio è veloce e permette all’acciaio di scaldarsi meno, subendo minori deformazioni termiche.
Il taglio autogeno o ossitaglio, invece, avviene attraverso la combinazione di gas, propano e ossigeno, che porta localmente l’acciaio ad un’elevata temperatura volatilizzando il carbonio.
Permette generalmente spessori maggiori (fino ai 600 mm) e, muovendosi lentamente, scalda maggiormente l’acciaio ma il risultato sui bordi è più preciso.
Una volta tagliato il pezzo, contestualmente al taglio o successivamente, in base alla tipologia di macchina, si esegue la marcatura,
ossia la punzonatura low stress (con minori impatti sulla lamiera, evitando principi di rottura e cricche) sulla lamiera tagliata del numero identificativo di ogni singolo elemento per permetterne l’identificazione e tracciabilità in ogni fase costruttiva.
2.3 Cianfrinatura
I singoli elementi verranno successivamente uniti insieme.
Quando l’unione avviene mediante saldatura, per assicurarne la corretta esecuzione si preparano i lembi alle estremità attraverso la cianfrinatura, ossia un particolare tipo di taglio angolato.
Lo spazio che si crea fra i lembi tagliati si chiama cianfrino ed agevola il riempimento dello spazio tramite metallo fuso d’apporto durante la saldatura.
Il cianfrino può essere di diversi tipi: a "v", a "u", a "doppia u", a "x", a "imbuto".
2.4 Foratura
Quando i singoli elementi verranno successivamente uniti mediante bullonatura o barre, i singoli elementi vengono preparati con i fori necessari ad accogliere il bullone.
La foratura è una lavorazione meccanica ad asportazione di truciolo e, in caso di fori ovali e non circolari, è necessario utilizzare un’alesatrice che, con un moto rotatorio, aumenta il diametro del foro e lo porta alla geometria ovale desiderata.
2.5 Travi saldate
Quando le dimensioni dei profilati commerciali superano quelle standard, le travi a doppio T vengono composte da lamiere e larghi piatti con spessori solitamente maggiore ai 12 mm saldati insieme con sistemi di saldatura automatici.
In questo modo è possibile ottenere delle sezioni costruite dalle forme e dimensioni altrimenti non ottenibili con la normale laminazione a caldo.
2.6 Steel preparation
In caso la struttura venga verniciata si procede con le attivià di steel preparation - molatura bordi, spigolatura angoli, svasatura fori, attività svolte in maniera automatica garantandone la qualità - con lo scopo di rifinire le pre-lavorazioni e favorire l’aderenza della vernicie che verrà applicata successivamente,
specie in aree della struttura come fori ed angoli dove, in futuro, è più probabile lo svilupparsi di ruggine.
I singoli elementi o posizioni vengono composti insieme attraverso il processo di lavorazione in marche, ossia elementi formati da diverse parti, secondo le specifiche di progetto.
3.1 Trasporto da altri stabilimenti
I singoli elementi pre-lavorati durante la precedente fase produttiva vengono smistati e trasportati verso altri stabilimenti per essere assemblati e lavorati in strutture composte.
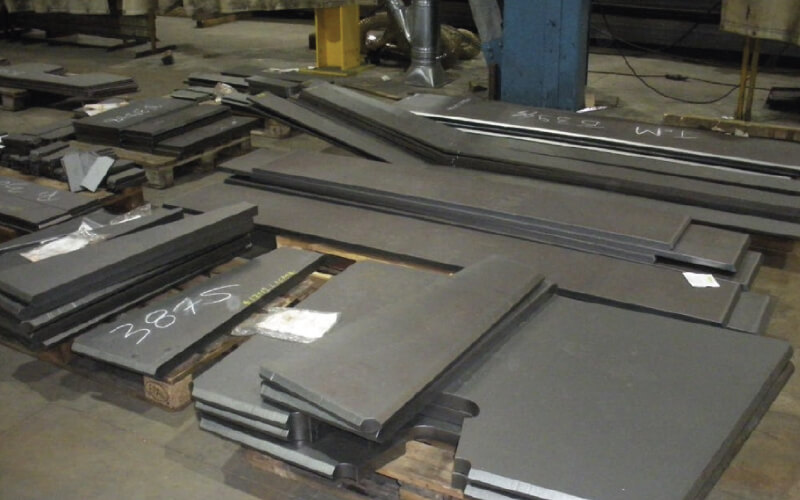
3.2 Assiemaggio
L’attività di imbastitura consiste nel montaggio provvisorio dei singoli elementi della struttura per fissare con precisione le posizioni relative degli elementi che la compongono tramite saldatura a punti utilizzando elettrodi/filo per la saldatura, onde permettere il successivo collegamento dei pezzi fino alla saldatura completa.
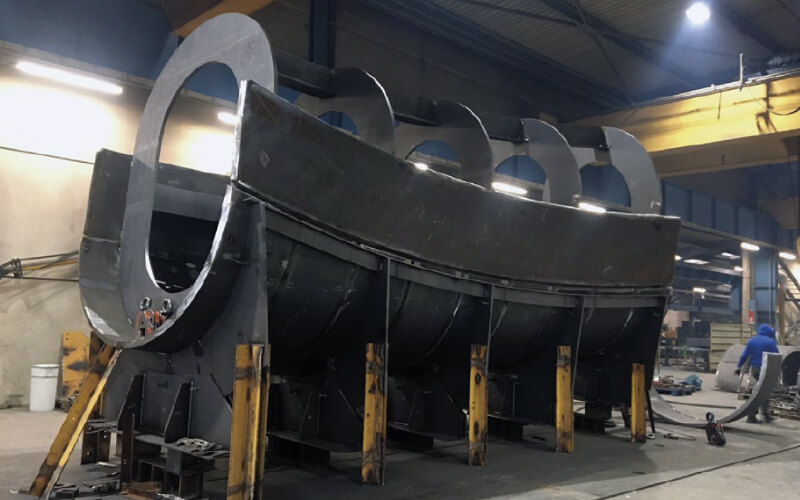
3.3 Saldatura
La saldatura è un processo che permette l’unione di due pezzi di acciaio con soluzione di continuità (vi è una continuità quasi totale nelle caratteristiche del materiale delle parti unite) mediante la fusione degli stessi o tramite metallo d’apporto fondendo insieme i lembi accostati dei pezzi da congiungere.
Nei casi di saldatura automatica, il materiale d'apporto viene applicato attraverso appositi macchinari ed è preferito in quei casi dove la saldatura è per lunghi tratti privi di interruzione.
Negli altri casi si predilige la saldatura manuale, in cui il materiale d’apporto viene applicato da un saldatore che regola manualmente la saldatrice e movimenta la sorgente di calore adattandosi alla conformazione del pezzo da saldare. In base alla posizione del giunto rispetto all’operatore, si possono identificare diverse posizioni di saldatura, come in piano, frontale, sopratesta, verticale e inclinata.
La tipologia di saldatura si può inoltre identificare secondo la sorgente termica con cui viene prodotto il calore che porta a fusione il metallo: nel caso di saldatura a gas,
la protezione del bagno di saldatura è assicurata da un gas di copertura che protegge la zona di saldatura dagli influssi dell’atmosfera circostante,
mentre nel caso di saldatura ad arco la fusione avviene grazie al raggiungimento di altissime temperature per mezzo di un "arco" elettrico che viene generato fra l’elettrodo e la parte da saldare, in cui l’elettrodo è fuso e il materiale si depositano lungo il giunto da riempire.
Al termine della saldatura, è possibile sia necessaria la molatura, ossia l’operazione di levigare, arrotare e lucidare mediante mola o molatrice la saldatura in eccesso, per livellare o riformare il profilo delle parti unite.
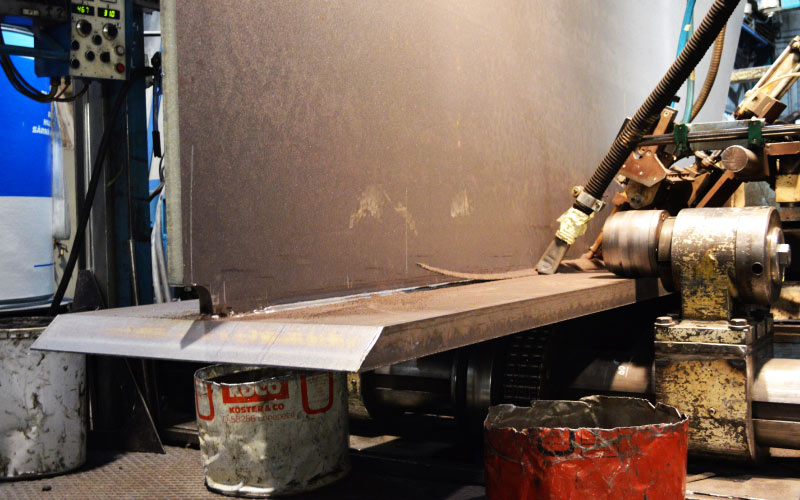
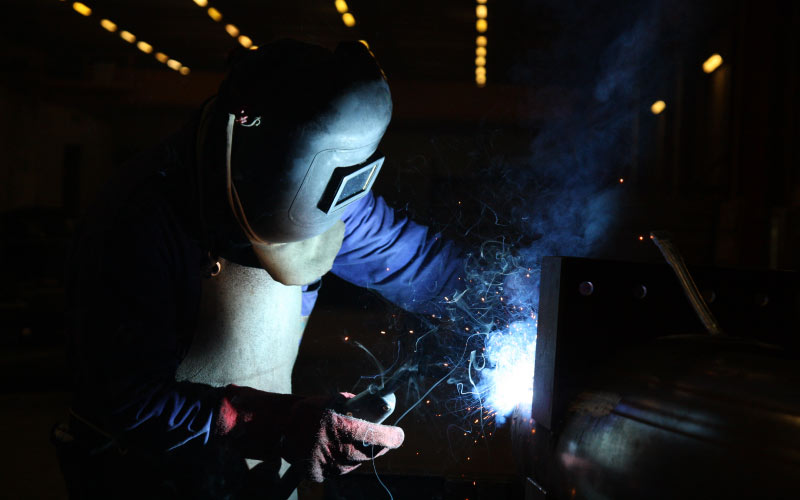
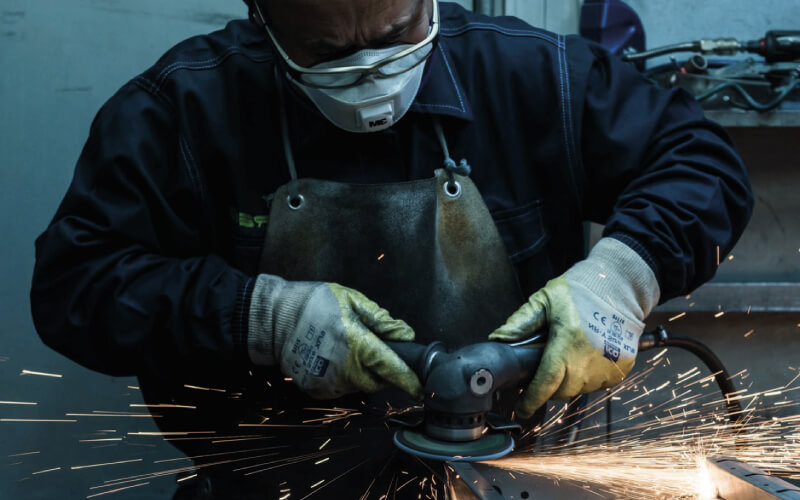
3.4 Piolatura
Processo di saldatura dei pioli connettori sulle travi tramite un sistema di saldatura a pressione: eseguita con la pistola, è realizzata facendo scoccare un arco elettrico tra la punta del prigioniero e la superficie dell’elemento metallico.
Sono impiegati soprattutto nelle strutture composte accio-calcestruzzo dei ponti per creare un effetto collaborante tra i due materiali attraverso la testa del piolo.

3.5 Pre-montaggio
Processo cui si uniscono opportunamente le parti di una struttura sulla base dei disegni di montaggio.
Viene svolto in officina, solitamente, quando la struttura è particolarmente complessa e si richiede il controllo delle geometrie complessive prima che la struttura venga trasportata in cantiere.
Si evitano in questo modo problemi di congruenza e si limitano gli imprevisti in cantiere, consentendo il contenimento dei costi di messa in opera.
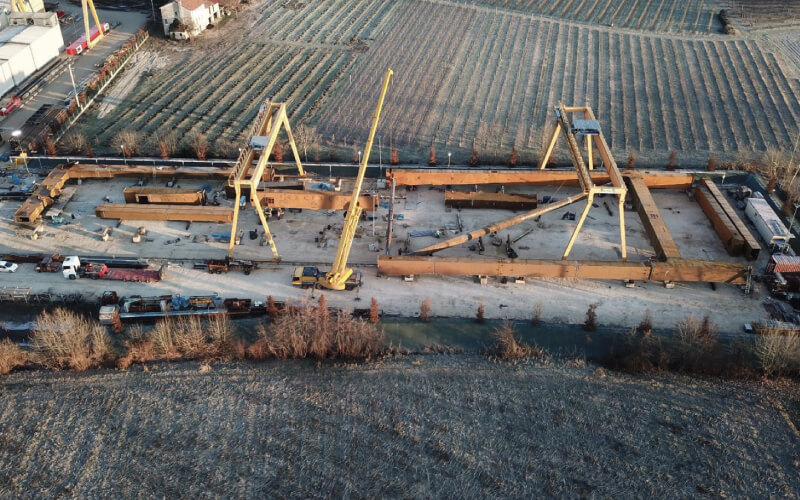
Determinato in base alla tipologia d’opera, all’utilizzo e alle condizioni atmosferiche a cui la struttura viene esposta, ha come obiettivo la protezione della struttura da ruggine e corrosione.
4.1 Verniciatura
La verniciatura consiste nell’applicazione di diversi strati di vernice per formare una superfice protettiva, il cui spessore è misurato in micron.
La verniciatura prevede, generalmente, i seguenti passaggi:
Sabbiatura: procedimento meccanico di abrasione della superfice tramite un getto di graniglia ed aria per rimuovere la calamina (l’ossido derivante dal taglio delle lamiere) e altre impurità erodendo la parte più superficiale dell’acciaio in modo da permettere la necessaria rugosità per dare alla vernice maggiore aderenza e presa. Quando gli elementi da sabbiare superano le dimensioni della sabbiatrice automatica, o in caso di specifica valutazione, la sabbiatura viene effettuata manualmente.
Applicazione: entro poche ore dalla sabbiatura è necessario procedere con la verniciatura onde evitare che il processo di ossidazione dell’acciaio ricominci. Il processo di verniciatura avviene manualmente, con una pistola ad aria compressa: si tratta infatti di superfici estremamente variegate e irregolari, impossibili da verniciare in maniera automatica. Lo spessore della verniciatura viene stabilita nelle caratteristiche di progetto dall’ufficio tecnico: in concomitanza con l’ufficio qualità e con il cliente, è stabilito lo spessore di verniciatura dell’opera, che viene calcolato sulla base della sua superficie della struttura e della classe di corrosività dell’ambiente.
Intumescente: se previsto, alla struttura può essere applicato uno strato di vernice intumescente la quale offre, ad elevata temperatura, la protezione contro il fuoco attraverso un processo di espansione dei componenti delle vernici stesse, creando uno strato microcellulare altamente coibente e resistente al calore. Questa viene applicata in cantiere con pompe airless specifiche, negli spessori atti a fornire una resistenza al fuoco R-REI che varia da 30 a 120 minuti, fornendo il tempo necessario per evacuare l’area in caso di incendio.
4.2 Zincatura
Processo con cui viene applicato un rivestimento di zinco su un manufatto metallico per proteggerlo dalla corrosione.
Innanzitutto, il materiale da trattare è adeguatamente preparato (pre-sgrassato, decapato e sgrassato), poi zincato per immersione a caldo (l’elemento da trattare viene completamente immerso nello zinco fuso che si trova ad una temperatura di circa 445 °C), o attraverso la zincatura elettrolitica (l’elemento viene immerso in una soluzione elettrolitica, contenente sali di zinco).
4.3 Naturale CorTen
La protezione dell’acciaio avviene attraverso la propria caratteristica auto passivante.
Questo tipo di acciaio è chiamato Corten dall’abbreviazione dei termini inglesi che ne definiscono le caratteristiche principali, CORrosion restistance (resistenza alla corrosione) e TENsile strength (resistenza a trazione), e presenta ruggine e scaglie di laminazione (calamina) che producono una patina auto proteggente.
Solitamente è sconsigliato in ambienti marini poiché impedisce la formazione della patina auto proteggente.
4.4 Trasposto verso cantiere
Gli elementi lavorati e trattati vengono trasportati verso il cantiere di destinazione per essere assemblati ed installati nella loro conformazione finale.
In base alla distanza e raggiungibilità del luogo, il trasporto può essere:
Via terra: attraverso bilici standard con 13.50 metri di rimorchio, trasporti con misure che eccedono questa lunghezza vengono definiti eccezionali e richiedono specifici permessi.
Via mare: trasporto intermodale in cui il materiale viene trasporto via gomma presso il porto di riferimento per essere trasportato via mare in container standard da 40 piedi (11.90x2.30x2.30 metri al netto di carico) oppure,
quando diventa necessario trasportare elementi fuori standard, si ricorre al trasporto eccezionale cosiddetto break-bulk, in cui non esistono limiti di fattibilità di trasporto e i pezzi, di notevoli dimensioni, vengono caricati singolarmente.
Viene poi essere scaricato a destinazione per raggiungere il cantiere nuovamente via gomma.
Via aerea: in casi eccezionali, per singoli elementi con poco peso, si può ricorrere ad una più veloce spedizione aerea.
L’insieme di quelle azioni, processi e relativi documenti lungo l’intero ciclo produttivo volti a garantire il raggiungimento della performance secondo i requisiti e gli standard richiesti.
5.1 Tracciabilità
L’intero processo produttivo si attiene alle normative sulla qualità vigenti, assicurando la tracciabilità del materiale e delle relative lavorazioni su tutta la filiera per comprovare la conformità della struttura assicurando l’ottemperanza alle normative lungo le diverse fasi. Oltre ai certificati da richiedere al fornitore sul materiale grezzo in fase di acquisto,
i quali certificano la conformità della fornituraall’ordine basandosi su controlli specifici a campione, vengono monitorate e certificate anche le successive lavorazioni secondo le specifiche di progetto.
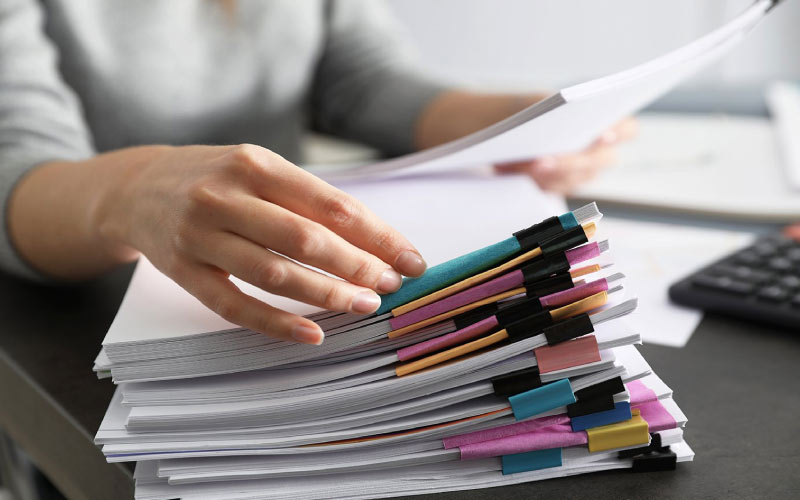
5.2 Controllo saldatura
Per verificare che non ci siano impurità all’interno della saldatura vengono eseguiti dei controlli sui giunti saldati.
Esistono diverse metodologie di Controlli Non Distruttivi (CND), e le normative di riferimento di ogni progetto stabiliscono il livello di controllo da garantire.
Controllo visivo: verifica la conformità alle specifiche geometriche del progetto per identificare eventuali distorsioni o presenza di difetti evidenti quali cricche, porosità, fusioni incomplete e altri difetti immediatamente visibili senza la necessità di ulteriori controlli.
Controllo magnetico (MT): consiste nel magnetizzare l’area sottoposta al test cospargendola, attraverso uno spray, di polveri magnetiche che vengono attirate nelle zone in cui sono presenti difetti superficiali o sub superficiali.
Controllo ad ultrasuoni (UT): consiste nell’introdurre nell’area sottoposta al test, attraverso una sonda, delle onde sonore ad alta frequenza per rilevare la presenza di eventuali difetti superficiali o interni, rilevabili dal rimbalzo delle onde sonore contro un eventuale ostacolo o difetto.
Le prove distruttive, al contrario, prevedono la distruzione della giunzione e necessitano quindi la realizzazione di appositi campioni di prova.
Lo scopo è principalmente quello di valutare le caratteristiche meccaniche (prove di trazione, di piega e di resilienza) oppure metallurgiche (macrografie o micrografie) del giunto.
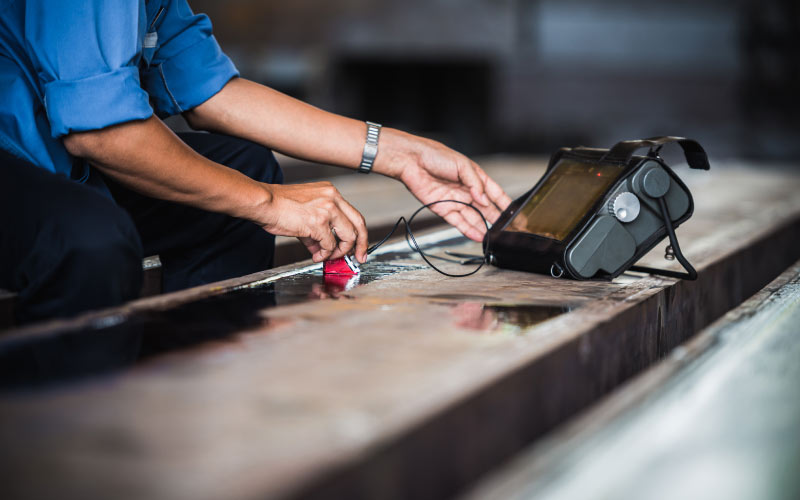
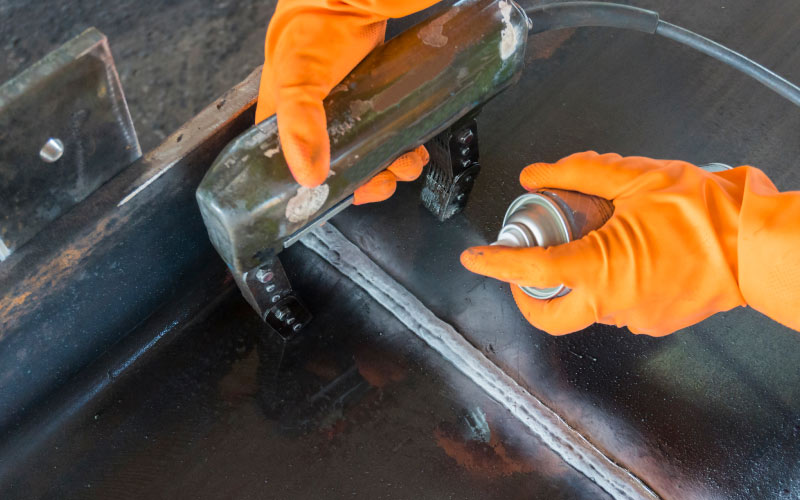
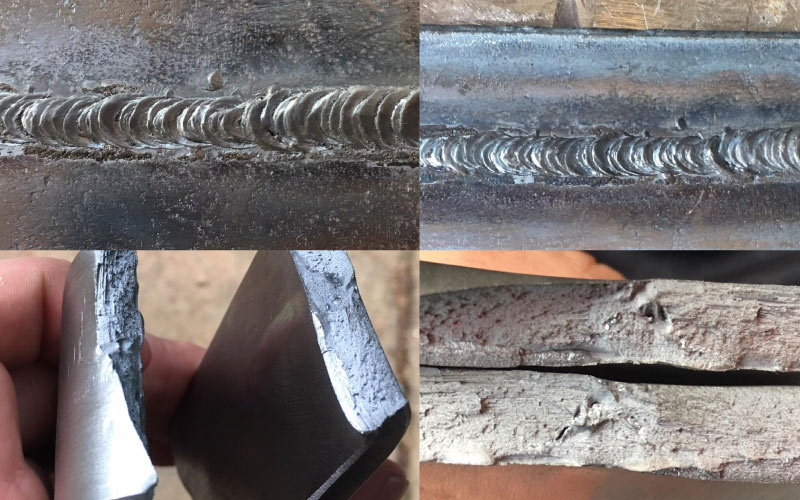
5.3 Controllo topografico
Un rilievo topografico consiste nell’acquisizione di misure e dati nello spazio effettuata per ottenere una rappresentazione grafica.
Durante l’assemblaggio di elementi singoli in strutture complesse è necessario assicurarsi che la geometria e la collocazione nello spazio dei vari elementi sia corretta, prima di procedere all’unione degli elementi mediante saldatura o bullonatura.
La topografia permette di rilevare i punti della struttura reale e di confrontarla con il modello per verificare eventuali scostamenti da correggere, assicurando la corretta geometria anche per strutture complesse.
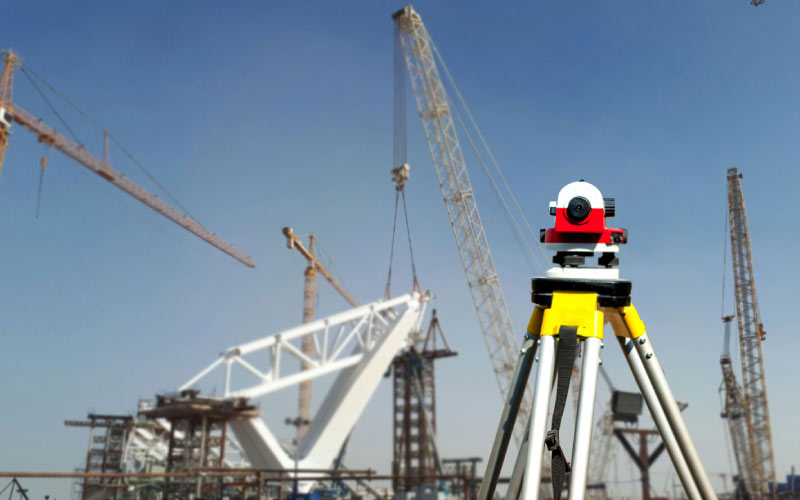
5.4 Controllo verniciatura
Per verificare la corretta applicazione della verniciatura, il giusto spessore in micron e fornire una garanzia della durata e della tenuta della vernice vengono effettuati dei microtest magnetici che misurano la distanza tra la superficie e lo strato in acciaio sottostante.
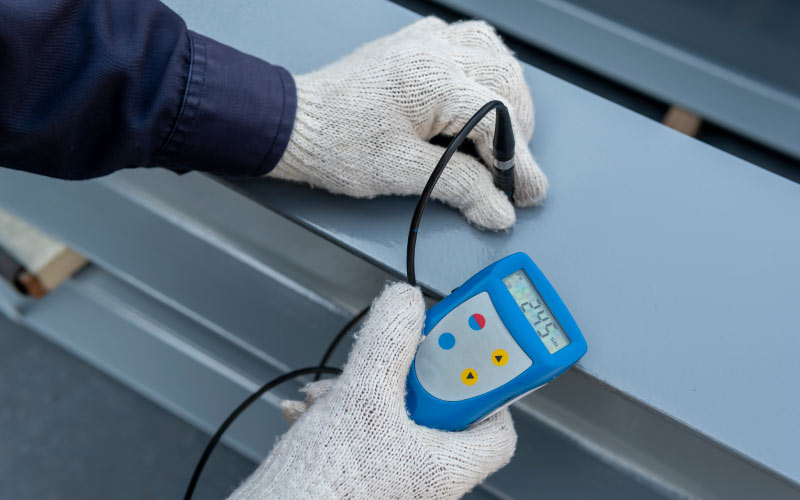
5.5 Controllo bullonatura
Per garantire il funzionamento di una unione bullonata, i bulloni devono essere adeguatamente serrati con chiave dinamometrica: non devono essere poco serrati, per ovvi motivi,
ma nemmeno eccessivamente serrati per evitare il rischio di snervamento o addirittura la rottura del bullone.
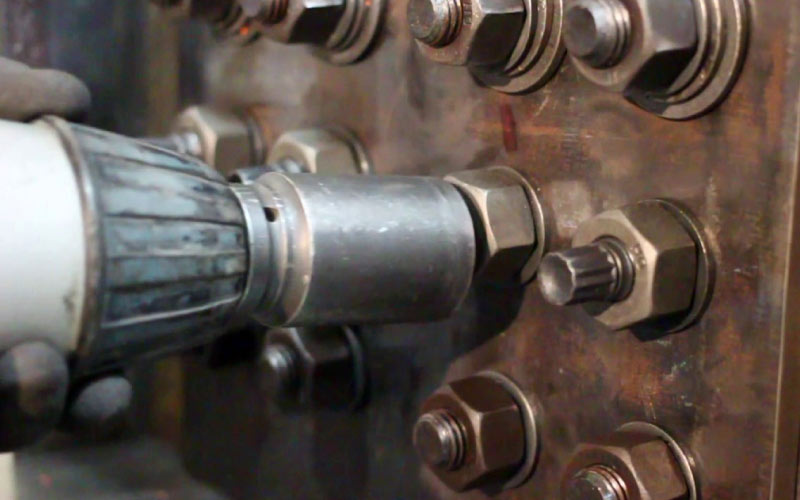
CREDITS
Photograph of the Brooklyn Bridge whilst under construction - World History Archive
Brooklyn Bridge and Manhattan skyline - Detroit Publishing Company
View from Crissy Field in the Presidio of the construction of the Golden Gate Bridge with the roadbed being installed - Underwood Archives/Getty Images
Living model illustrating principle of the Forth Bridge - Wikipedia
Forth Bridge - A London Inheritance
The Statue of Liberty during construction - Horace Abrahams/Getty
Construction of the Eiffel Tower - Roger Viollet/Contributor/Getty
The Woodroot brothers and their shawl collared sweaters - Property of the Auburn University Libraries
PARTNER
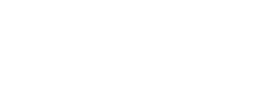
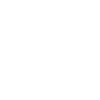