Grande beauté et ingéniosité technique représentent les qualités distinctives qui permettent à une œuvre architecturale de devenir une icône, une figure emblématique, destinée à traverser les siècles en laissant une trace indélébile dans la société.
Avec leur style unique, les grands œuvres ont toujours exercé un attrait magnétique sur l’homme. Leurs formes iconiques et incomparables sont entrées dans l’imaginaire collectif à travers des centaines de films et de photographies, se transformant en symbole de villes et de nations.
Mais derrière chaque grande œuvre se cache toujours une grande histoire, et avec elle de nombreuses questions. Quels sont les éléments qui la composent ? Comment sont-ils réalisés ? Et quelles sont les étapes techniques qui permettent à l’œuvre de résister dans le temps ?
Maeg ouvre les portes de ses bureaux et de ses établissements, en racontant les étapes qui marquent le cycle productif de ses projets: bienvenue dans les coulisses du monde Maeg, où technique et passion s’unissent pour donner vie à des œuvres destinées à durer dans le temps.
Processus à la base d’un projet pour définir, en se basant sur des normes, calculs, spécifications techniques et dessins, chaque détail de la structure en termes de production et installation de l’œuvre.
1.1 Analyse de la documentation
Le processus de conception commence avec l’analyse des informations sur le projet du client, qui peut être un avant-projet – établit les caractéristiques plus importantes à développer en détail- soit un projet exécutif dans lequel les caractéristiques du matériau, des dimensions et géométriques de la structure sont déjà spécifiées.
Une partie intégrante de la documentation est composée par les spécifications techniques et le cahier (CCTP), c’est-à-dire les références légales destinées à identifier les exigences de l’ouvrage en termes de qualité, traitement superficiel et classe d’exécution.
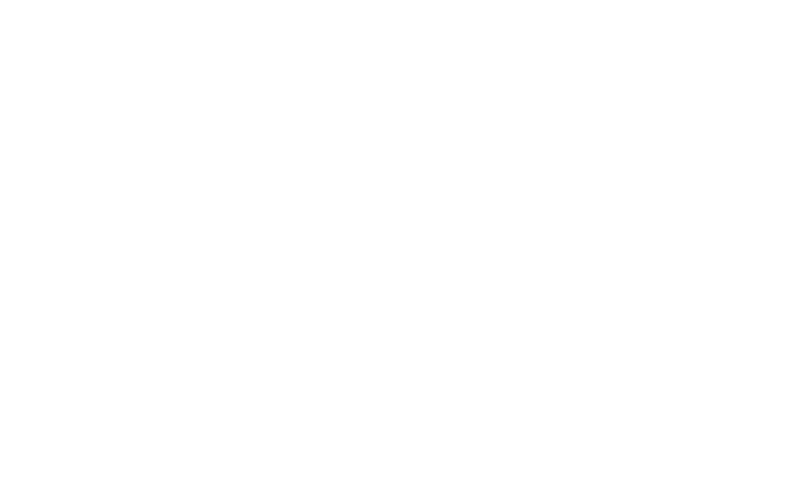
1.2 Développement pour la production
Le projet de l’œuvre est remodelé en analysant chaque détail pour réaliser des schémas structurels dans lequels, pour chaque élément constituant la structure, sont définis les détails comme la géométrie, les trous, les épaisseurs, les chanfreins, les soudures et le numéro de pièces à produire en identifiant ensuite chaque élément par un numéro d’identification.
Ayant défini chaque élément de la structure, grâce à l’élaboration des schémas structurels on obtient là les metrés, c’est-à-dire une liste qui synthétise le besoin, la qualité et les dimensions du matériau à approvisionner pour le projet.
Pour chaque position, sont reportées dans un manuel les différentes phases du processus de production, de façon à effectivement commencer la phase de production.
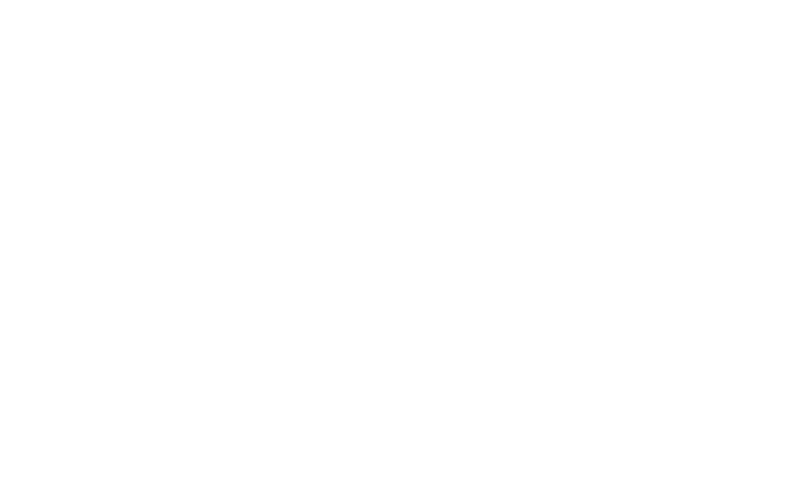
1.3 Développement pour le chantier
Une fois analysés les différents éléments qui composent la structure permettant de commencer la production, une phasage-procédure de montage pour établir les modalités et la séquence pour unir ces différents éléments ou éléments composés est étudié, tenant compte de la dimension, la constructibilité, la transportabilité, la disposition et les espaces dans le chantier et enfin les capacités de soulèvement des grues et de montage dans le chantier.
En prenant en compte les variables, on commence par réaliser un modèle de calculs pour vérifier résistence structurelle de l’ouvrage durant les différentes étapes de construction.
En développant les différentes phases, sont définis les équipements temporaires nécessaires durant la phase d’installation (structure de support, tours temporaires, etc. pour lesquels sont réalisés des schémas structurels et des notes de calcul pour ensuite commencer à les produire) et les moyens de soulèvement et transport nécessaires (grues, barges, etc., à approvisionner).
Une fois identifiée la méthode d’installation qui sera suivie pour la réalisation de l’ouvrage, le service technique rédige une procédure de montage illustrant les différentes phases assurant le respect des règles de sécurité.

APPROVISIONNEMENT
Le processus commercial qui assure les fournitures nécessaires pour satisfaire les besoins et les exigences pour la réalisation du projet d’après la liste des matériaux développée par le service technique.
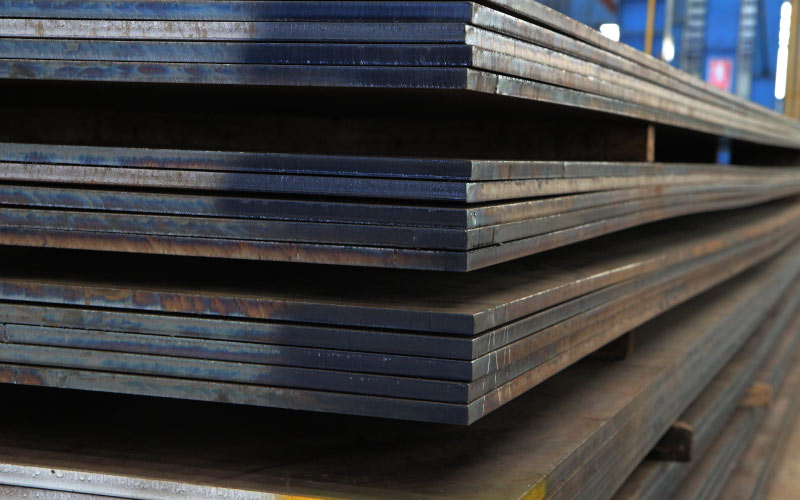
TÔLES
Les tôles sont des plaques d’acier obtenues grâce au processus de laminage de brames (produits semi-finis réalisés par des jets de coulée de métal liquide en formes spécifiques) dans lesquelles le matériau est passé à travers deux cylindres qui l’aplatissent jusqu’à obtenir l’épaisseur désirée.
PROFILÉS
Les profilés sont des produits étirés à chaud appelés « commerciaux » car ils respectent des normes internationales en matière de forme de la section de la barre.
Les poutres transversales plus communes sont :
Poutres « à double T »: profilés constitués de deux semelles parallèles liés perpendiculairement par une âme.
Ces profils peuvent être de différents types : IPE (la hauteur de l’âme est environ le double que la largeur de la semelle) ou HE (où l’âme et la semelle ont la même dimension).
Quand les dimensions des profilés dépassent celles standard, les poutres « à double T » sont composées de tôles soudées.
PROFILÉS
Poutres à « U » ou « C »: profilés constitués par un liner et deux semelles rejoints à l’une des deux extrémités, le type le plus commun est l’UPN.
Poutres à « L » ou angulaires: profilés constitués de deux bras perpendiculaires, appelés « à ailes égales » si de même longueur ou « à ailes inégales » si de longueur différente.
PRODUITS CREUX
Tubes ronds, obtenus à travers extrusion ou soudage longitudinale, ou bien tubes carrés ou rectangulaires, obtenus par pliage et successif soudage ou tréfilage.
CONNECTEURS
Connecteurs utilisés surtout dans les structures des ponts composées d'un mélange d'acier et béton, pour créer un effet collaborant entre les deux matériaux à travers la tête de connecteur, qui a un diamètre effectif supérieur à celui de la tige.
BOULONS
Éléments d'assemblage amovibles, généralement formés à partir d'un élément mâle (vis), d'un élément femelle (écrou) et une ou plusieurs rondelles, utilisées pour améliorer le verrouillage et distribuer la charge de serrage sur une surface plus grande.
En plus de la taille, les boulons se différencient par la classe de résistance: habituellement sont utilisés ceux de classe 8.8 (haute résistance) et 10,9 (très haute résistance).
PEINTURE
Tenant compte de la surface de la structure et de l’environnement naturel dans laquelle elle est installée, la quantité nécessaire est calculée et on procède à l’approvisionnement.
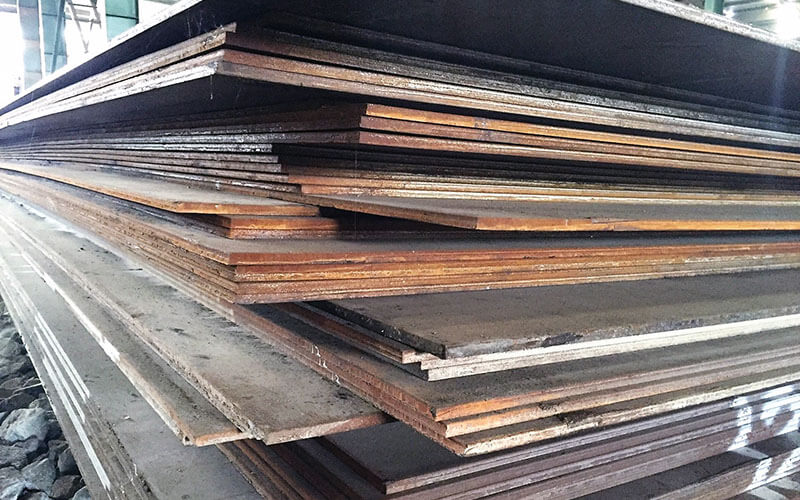



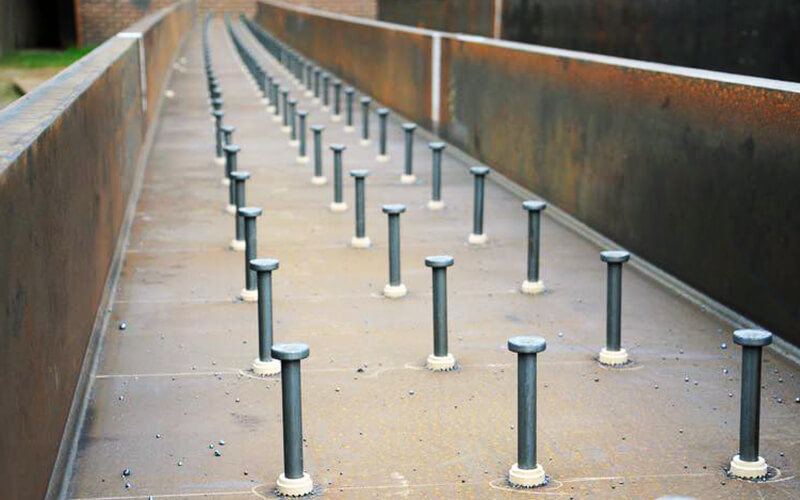
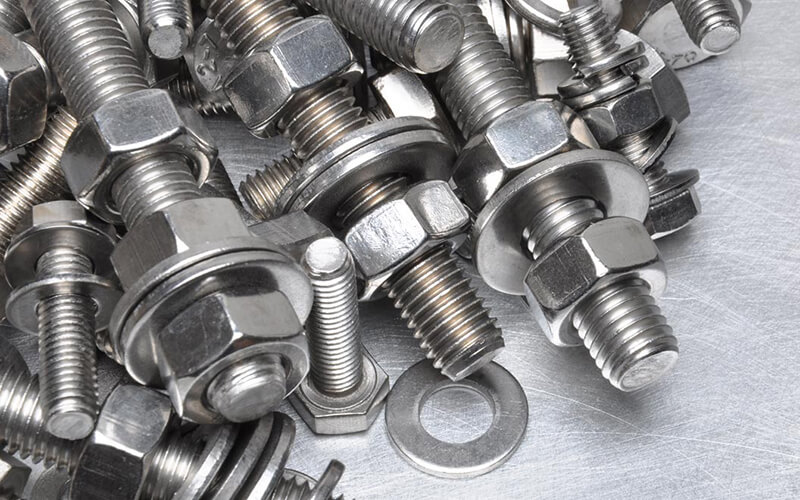

Les activités de pré-transformation consistent dans la réalisation des différents éléments de la structure grâce à l’aide de machines à contrôle numérique (ou CNC- Computer Numerical Control).
2.1 Acceptation des matériaux et nesting
La matière première est envoyée à l'usine et vient triée en fonction des priorités de production dans la zone de stockage et transportée dans les travées de production à l'aide de traverses magnétiques.
Le début des activités prévoit l'analyse du plan de coupe ou de nesting, c'est-à-dire l’analyse pour l'optimisation de la découpe de pièces façonnées des tôles minimisant les chutes (ou déchets de production) selon les normes du bureau technique: le nesting stocke les données de chaque marque telles que les dimensions, l'épaisseur et les processus associés.
2.2 Coupe
Une fois que le plan de coupe est établi, la phase de coupe proprement dite commence sur les tôles, les tubes et les angles.
La coupe peut être réalisée au plasma en ionisant l'air entre la torche et la tôle, créant une flamme qui atteint 20 000°C et pulvérise l'acier.
Généralement, les épaisseurs de coupe sont limitées, la coupe est donc rapide et permet à l'acier de chauffer moins, en subissant moins de déformation thermique.
Le coupe autogène ou oxycoupage, en revanche, se fait par la combinaison de gaz, de propane et d'oxygène, qui amène localement l'acier à une température élevée en volatilisant le carbone.
Il permet généralement des épaisseurs plus importantes (jusqu'à 600 mm) et, en se déplaçant lentement, il chauffe davantage l'acier, mais le résultat sur les bords est plus précis.
Une fois la pièce découpée, en même temps que la coupe ou plus tard, selon le type de machine, le marquage est effectué,
c'est-à-dire un poinçonnage à faible contrainte (avec moins d'impact sur la tôle, évitant les cassures et les fissures) sur la tôle découpée du numéro d'identification de chaque élément individuel pour permettre son identification et sa traçabilité dans chaque phase de construction.
2.3 Chanfreinage
Par la suite, les éléments individuels sont assemblés. Lorsqu’ils sont assemblés par soudage, afin d'assurer une bonne exécution, les bords sont préparés par chanfreinage, c'est-à-dire un type particulier de coupe angulaire.
L'espace qui est créé entre les bords coupés est appelé chanfrein et facilite le remplissage de l'espace au moyen de métal en fusion pendant le soudage.
Le chanfrein peut être de différents types : « V », « U », « Double U », « X » et « Y ».
2.4 Perçage
Quand les différents éléments sont ensuite assemblés par boulonnage ou tiges, ils sont préparés avec des trous pour accueillir le boulon.
Le perçage est une opération mécanique qui vise retirer les copeaux; en cas de trous ovales et non circulaires, il est nécessaire d’utiliser une aléseuse qui, grâce à un mouvement de rotation, augmente le diamètre du trou et produit la forme ovale souhaitée.
2.5 Poutres soudées
Lorsque la taille des profilés dépasse la norme, les poutres à double T sont composées de tôles ou de grandes plaques d'une épaisseur généralement supérieure de 12 mm, soudés ensemble par des systèmes de soudage automatiques.
De cette façon, il est possible d'obtenir des profilés de formes et dimensions autrement non réalisables par laminage à une chaleure régulière.
2.6 Préparation de l’acier
Au cas où la structure est peinte, l'acier est préparé par meulage des bords, arrondis des angles, fraisage de trous, toutes activités effectuées automatiquement en garantissant une certaine qualité, avec le but de raffiner la préproduction et de promouvoir l’adhérence de la peinture qui sera appliquée après, notamment dans des zones de la structures telles que les trous et les angles où la rouille est plus susceptible de se développer en futur.
Les différents éléments ou positions sont composés ensemble à travers le processus de fabrication en marques, c’est-à-dire des éléments composés de différentes parties, selon les spécifications du projet.
3.1 Transport à partir d’autres usines
Les différents éléments préfabriqués durant la phase de production précédente sont triés et transportés vers d’autres usines pour être assemblés et travaillés dans des structures composées.
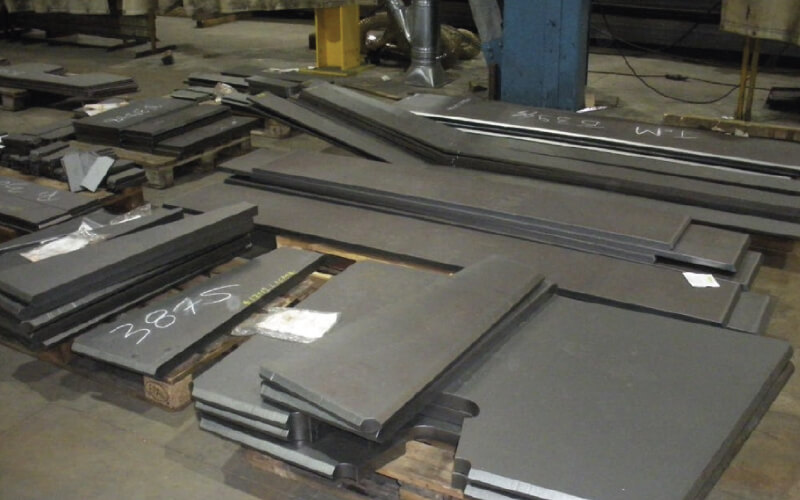
3.2 Assemblage
Le pointage consiste dans le fait de monter provisoirement différents éléments de la structure pour fixer avec précision les positions relatives des éléments qui la composent grâce au soudage par points en utilisant des électrodes/fils pour la soudure, afin de permettre ensuite l’assemblage des pièces jusqu'à la soudure complète.
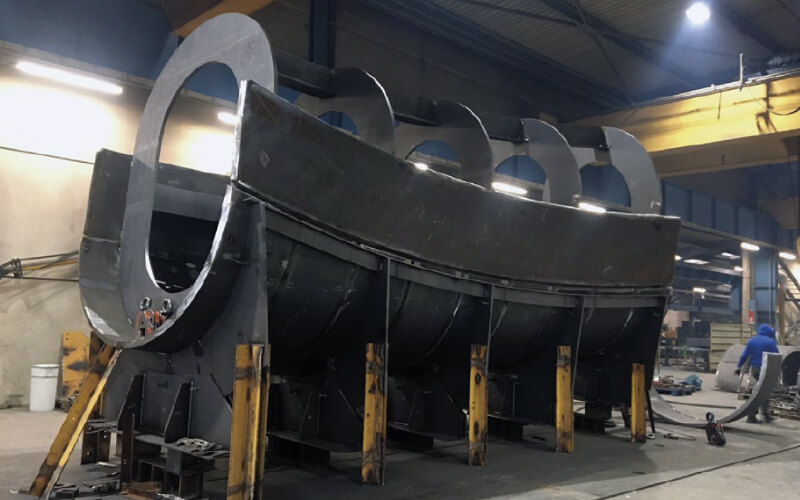
3.3 Soudage
Le soudage est un processus qui permet l’union de deux pièces d’acier avec solution de continuité (il y a une continuité presque totale dans les caractéristiques du matériau des pièces jointes) à travers la fusion de ces derniers ou grâce à un métal d’apport en fondant conjointement les bords mis côte à côte des pièces à unir.
Dans les cas de soudure automatique le matériau d’apport est appliqué à travers des machines spécialisées et il est préféré dans ces cas-là où la soudure est sans interruption sur de longues portions.
Dans les autres cas, le soudage manuel est privilégié. Le matériel d’apport est appliqué par un soudeur qui règle manuellement la soudeuse et manipule la source de chaleur. En fonction de la position du joint par rapport à l’opérateur on peut repérer plusieurs positions de soudage: à plat, frontale, au plafond, verticale, inclinée.
Le type de soudure peut aussi se repérer en fonction de la source thermique avec laquelle est produite la chaleur qui conduit à la fusion du métal: dans le cas du soudage au gaz, la protection du bain de fusion est assurée par un gaz de protection qui protège la zone de soudure de l’atmosphère environnante alors que dans le cas d’un soudage à l’arc la fusion a lieu grâce à l’obtention d’une très haute température à l’aide d’un « arc » électrique qui est généré entre l’électrode et la partie à souder dans laquelle l’électrode est fondue et le matériau se dépose le long du joint à remplir.
À la fin du soudage il est possible que nous ayons besoin du meulage, c’est-à-direct le besoin de poncer, d’aiguiser et de polir, grâce à une meule ou meuleuse, la soudure excédante pour niveler ou modifier le profil des parties jointes.
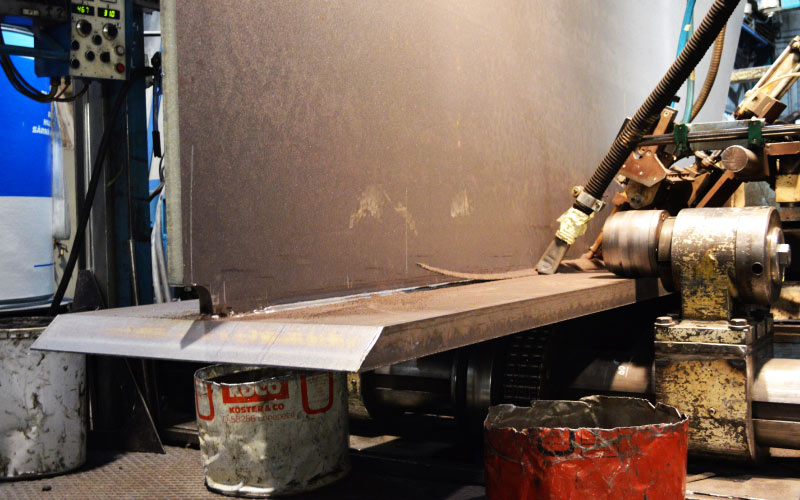
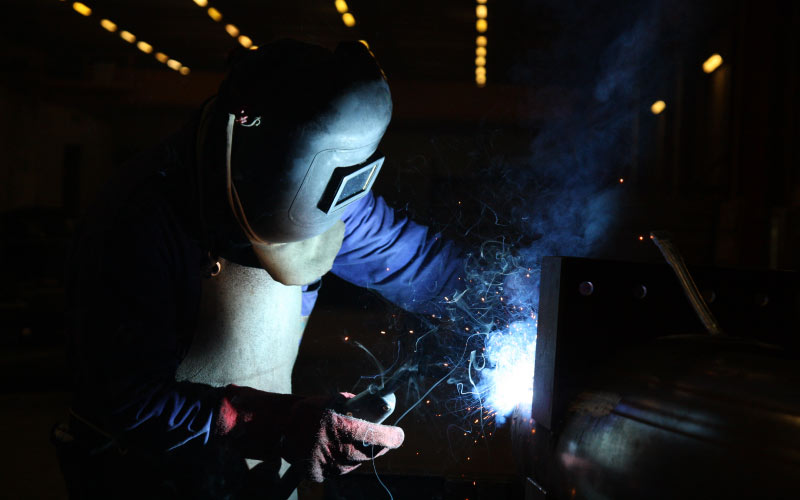
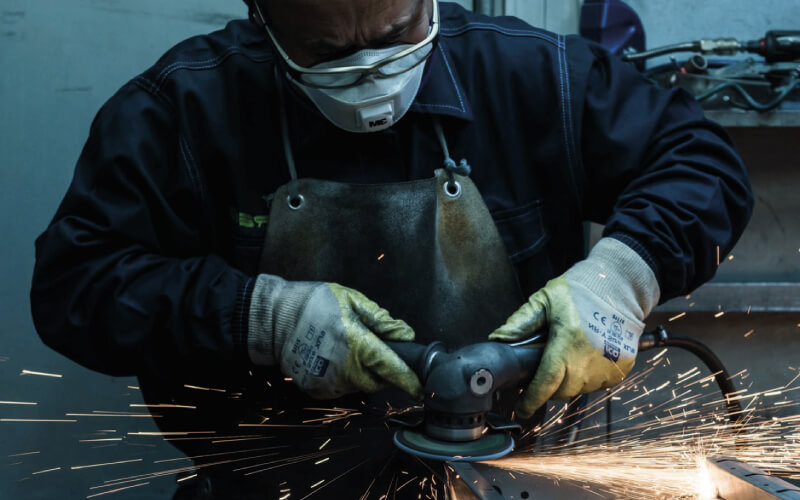
3.4 Pose des connecteurs
Processus de soudage des connecteurs sur les poutres grâce à un système de soudage à pression: effectué avec un pistolet, il est réalisé en faisant décocher un arc électrique entre la pointe de l’ustensile et la surface de l’élément métallique.
Sont utilisés surtout dans les structures composées de béton armé des ponts pour créer un effet collaborant entre les deux matériaux à travers la tête du connecteur.

3.5 Montage a blanc
Processus dans lequel s’unissent opportunément les parties d’une structure sur la base des plans de montage.
Il est effectué en atelier, généralement, quand la structure est particulièrement complexe et il est nécessaire de contrôler les géométries totales avant que la structure ne soit transportée en chantier.
Ainsi on évite des problèmes de congruence et on limite les imprévus en chantier en permettant la réduction des coûts de mise en œuvre.
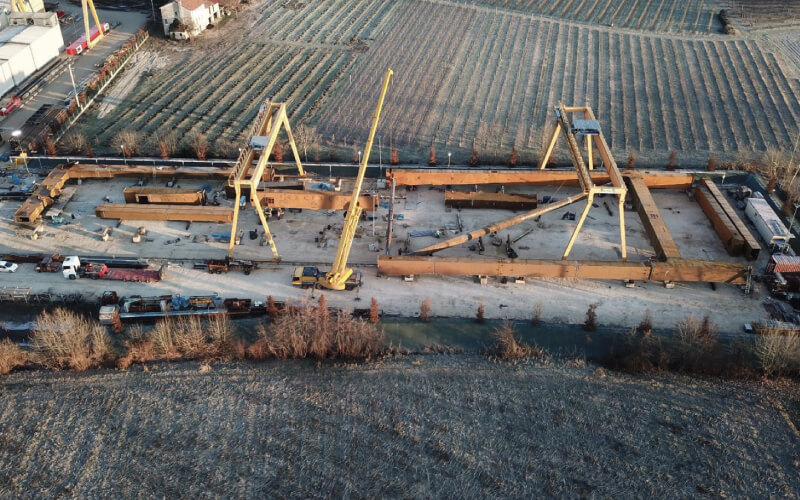
Déterminé en fonction du type d’ouvrage, à l’utilisation et aux conditions atmosphériques auxquelles la structure est exposée, vise à protéger la structure contre la rouille et la corrosion.
4.1 Peinture
Consiste en l'application de plusieurs couches de peinture pour former une surface de protection dont l'épaisseur est mesurée en micromètres.
Le revêtement implique généralement les étapes suivantes:
Sablage: un processus mécanique d'abrasion de la surface par un jet de sable et air pour éliminer la calamine (oxyde issu de la découpe des feuilles) et d'autres impuretés en érodant la partie la plus superficielle de l'acier, pour permettre une rugosité de la surface qui garantit une adhérence plus efficace de la peinture. Lorsque les éléments nécessitant un sablage dépassent les dimensions de la sableuse automatique, ou en cas d'évaluation spécifique, le processus de sablage est effectué manuellement.
Application: il est nécessaire de procéder à la peinture dans les quelques heures suivant le sablage, pour empêcher le processus d'oxydation de l'acier de redémarrer. La peinture se fait manuellement avec un pistolet à air comprimé: les surfaces sont en fait extrêmement variées et irrégulières et il serait impossible de le peindre automatiquement. L'épaisseur de la couche de peinture est établie dans les caractéristiques étudiées par le bureau technique avec le client et calculée sur la base de la surface de la structure et de la corrosion de l’environnement.
Intumescent: si nécessaire, une couche de peinture intumescente peut être appliquée sur la structure qui, à des températures élevées, offre une protection contre le feu grâce à un processus d'expansion des composants de la peinture elle-même, créant une couche micro cellulaire hautement isolante et résistante à la chaleur. Cette peinture intumescente est appliquée sur site avec des pistolets « airless » particulières, d'une épaisseur adaptée pour assurer une résistance au feu R-REI variant de 30 à 120 minutes, laissant le temps nécessaire pour évacuer la zone en cas d'incendie.
4.2 Galvanisation
Un processus dans lequel un revêtement de zinc est appliqué sur un élément métallique pour le protéger de la corrosion.
Tout d'abord, le matériau à traiter est adéquatement préparé (pré-dégraissé, décapé et dégraissé), puis galvanisé par bain à chaud (l'élément à traiter est complètement immergé dans le zinc fondu à une température d'environ 445 ° C), ou par galvanisation électrolytique (l'élément est immergé dans une solution électrolytique contenant des sels de zinc).
4.3 CorTen
La protection de l'acier se produit par sa propre caractéristique auto patinable.
Ce type d'acier est appelé CorTen, de l'abréviation des termes anglais qui définissent ses principales caractéristiques, la résistance à la corrosion et la résistance à la traction, et il présente une couche de rouille auto protectrice.
Il n'est généralement pas recommandé dans les environnements marins car cela empêche la formation de la patine auto protectrice.
4.4 Transport vers chantier
Les éléments, produits et traités, sont transportés sur le site de destination pour être assemblés et installés dans leur disposition finale.
Selon la distance et l’accessibilité du lieu, le transport peut être:
Par voie terrestre: via des camions standard avec une remorque de 13,50 mètres, transports avec des mesures dépassant cette longueur sont classées comme non standard et nécessitent des permis spécifiques.
Par mer: transport intermodal dans lequel le matériel est transféré par route jusqu'au port de référence pour être ensuite transporté par mer dans des conteneurs standard de 40 pieds (11,90 x 2,30 x 2,30 mètres nets de charge) ou, lorsqu'il est nécessaire d'expédier éléments non standard, le soi-disant break-bulk est utilisé comme un mode de transport exceptionnel, qui n'a pas de limites de faisabilité de transport et les pièces qui sont considérablement volumineuses sont chargées individuellement.
Une fois à destination le matériel est déchargé pour rejoindre à nouveau le chantier par la route.
Par avion: un transport aérien plus rapide peut être utilisé dans des cas exceptionnels concernant des éléments légers.
L’ensemble des actions, processus et document qui, durant tout le cycle de production visent à assurer la réalisation des performances selon les exigences et les normes requises.
5.1 Traçabilité
L'ensemble du processus de production est conforme aux normes de qualité actuelles, garantissant la traçabilité des matériaux et des processus associés tout au long de la chaîne d'approvisionnement.
Cela est nécessaire pour prouver la conformité de la structure et assurer le respect des réglementations le long des différentes étapes.
En plus des certificats de matières premières à être demandés au fournisseur lors de l'achat, qui certifient la conformité des fournitures à la commande se basant sur des contrôles d'échantillons spécifiques, les ouvraisons suivantes sont monitorées et certifiées également selon les spécifications du projet.
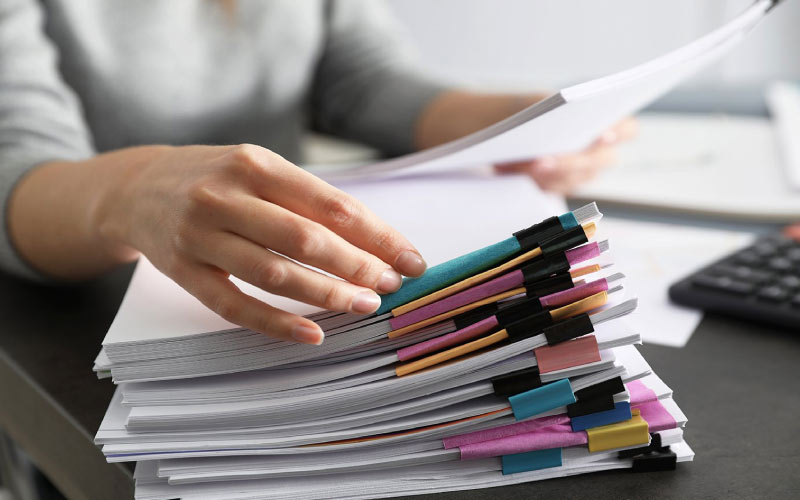
5.2 Inspection de la soudure
Afin de vérifier l'absence d'impuretés à l'intérieur de la soudure, des contrôles sont effectués sur les joints soudés.
Il existe différentes méthodologies de contrôle non destructif et des normes de référence pour chaque projet établissent le niveau de contrôle à garantir.
Contrôle visuel: il vérifie le respect de la spécification géométrique du projet, des distorsions possibles et la présence d'irrégularités évidentes telles que des fissures, porosités, fusions incomplètes et autres défauts visibles.
Contrôle magnétique: un champ magnétique est créé sur la soudure, qui est saupoudrée de poudres magnétiques, puis un spray contenant des particules métalliques est utilisé: la concentration de poudre métallique correspond à la présence de défauts, qui deviendront visibles grâce au spray.
Ce type d'inspection est effectué sur les soudures à cordon d'angle.
Contrôle par ultrasons: à l'aide d'une sonde, des ondes sonores haute fréquence sont introduites à travers le matériau à examiner, afin de mettre en évidence des défauts superficiels et internes, mesurer l'épaisseur des matériaux, ainsi que la position et la taille des défauts.
Ce type d'inspection est effectué sur des soudures à pleine pénétration.
Au contraire, les tests destructifs impliquent la destruction de la jonction et donc ils nécessitent la production d'échantillons de test spécifiques.
L’objectif est principalement d’évaluer les tests mécaniques (essais de traction, flexion et résilience) ou métallurgiques (macrographies ou micrographies) caractéristiques de l'articulation.
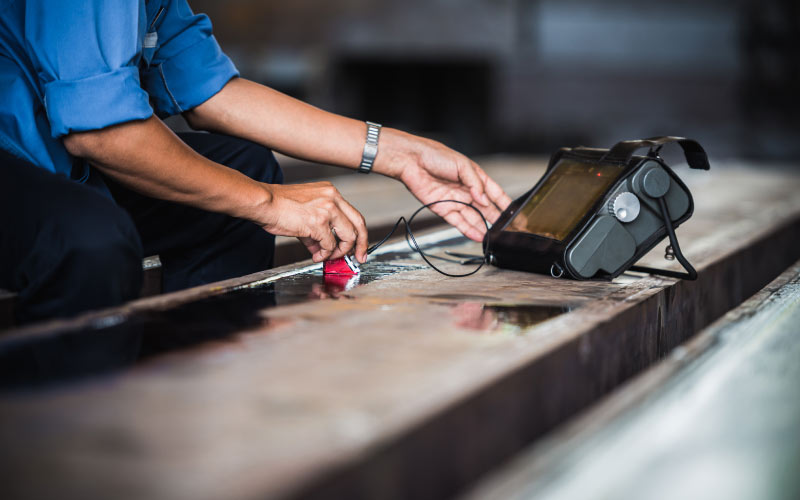
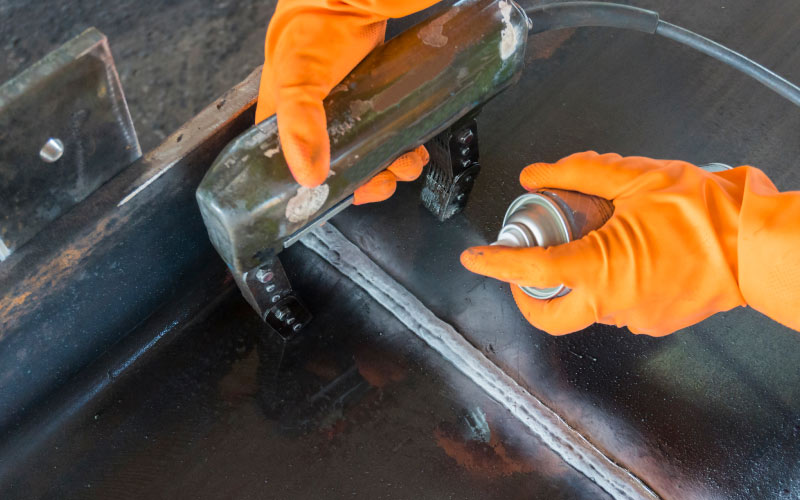
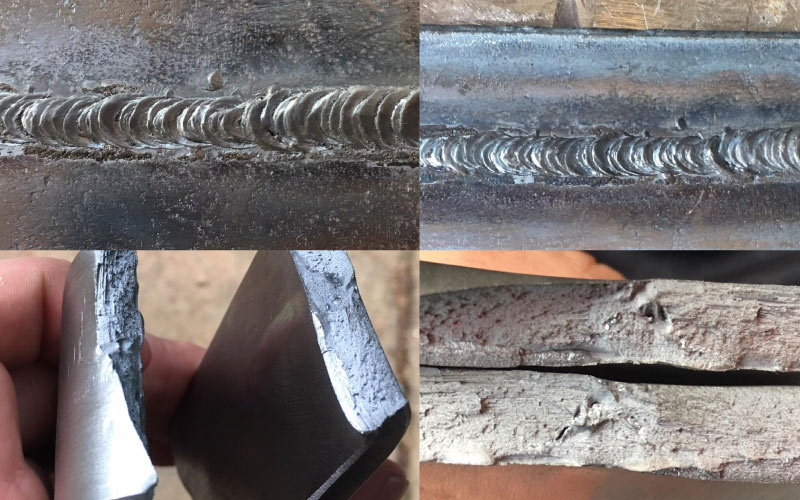
5.3 Inspection topographique
Une analyse topographique consiste à acquérir les mesures et données de l'espace réalisées pour obtenir une représentation graphique.
Lors de l'assemblage d'éléments uniques dans des structures complexes, il est nécessaire d'assurer la géométrie et la position correctes des différents éléments dans l'espace, avant de procéder au soudage et au boulonnage.
L'inspection topographique permet de détecter les coordonnées de la structure réelle et de les comparer avec le modèle, en vérifiant les écarts à corriger, en préservant la bonne géométrie même pour les structures complexes.
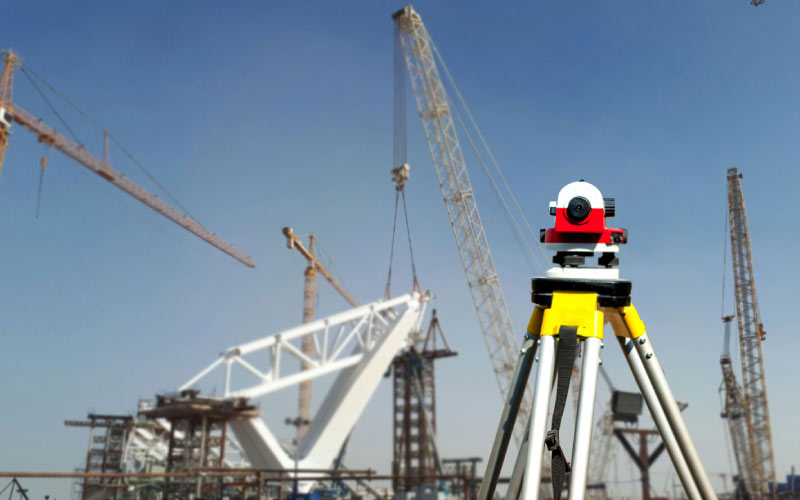
5.4 Inspection de la peinture
Des micro-tests magnétiques sont effectués pour vérifier la bonne application de la peinture et la bonne épaisseur en microns, ainsi que pour garantir la durabilité et l'étanchéité de la peinture.
Les micro-tests magnétiques peuvent mesurer la distance entre la surface l’acier.
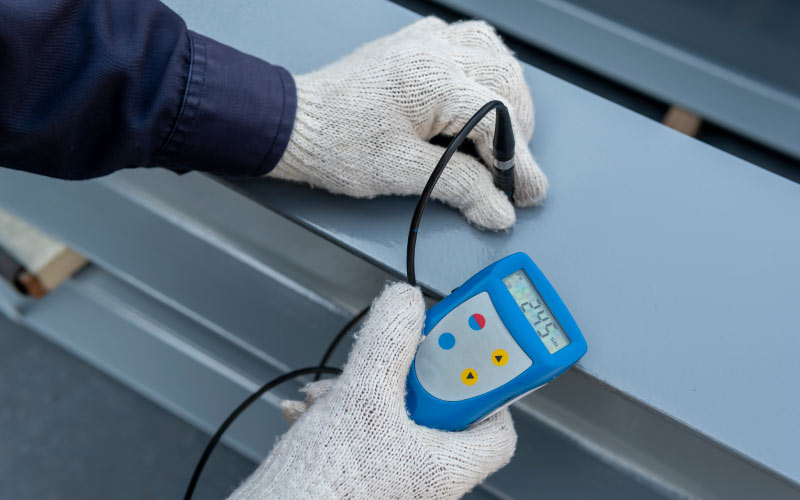
5.5 Inspection du boulonnage
Pour garantir le fonctionnement d’une jonction boulonné, les boulons doivent être serrés avec précision à l’aide d’une clé dynamométrique: pour des raisons évidentes,
ils ne doivent ni être serrées légèrement, mais ni trop serrées, pour éviter le risque d’écoulement voire de casser le boulon.
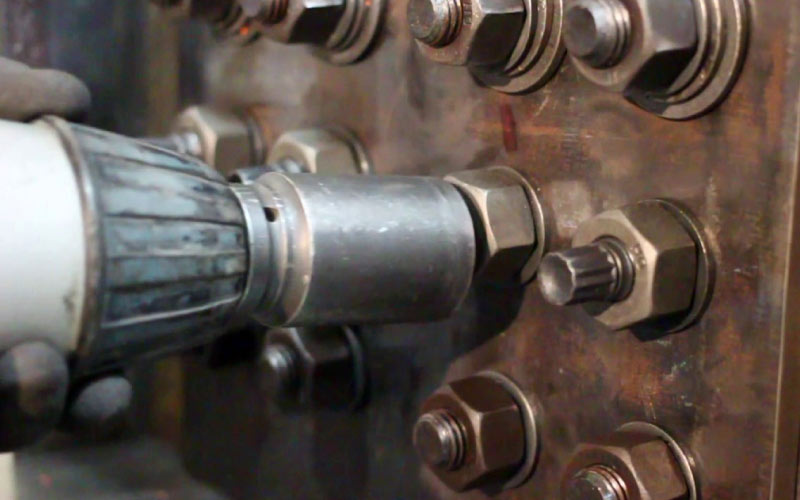
CREDITS
Photograph of the Brooklyn Bridge whilst under construction - World History Archive
Brooklyn Bridge and Manhattan skyline - Detroit Publishing Company
View from Crissy Field in the Presidio of the construction of the Golden Gate Bridge with the roadbed being installed - Underwood Archives/Getty Images
Living model illustrating principle of the Forth Bridge - Wikipedia
Forth Bridge - A London Inheritance
The Statue of Liberty during construction - Horace Abrahams/Getty
Construction of the Eiffel Tower - Roger Viollet/Contributor/Getty
The Woodroot brothers and their shawl collared sweaters - Property of the Auburn University Libraries
PARTNER
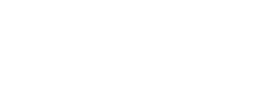
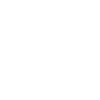